Overalls, Dungarees, Work Shirts, and More:
The Iconic Brand that is L.C. King
Written by Marianne Leek / Photography by Briana Fillers
For 110 years, L.C. King Manufacturing has made durable workwear and streetwear of unmatched quality and craftsmanship, and for the past 25 years Jack King, the great-grandson of Landon Clayton King, has been at the helm of the company and remained committed to his family’s legacy of excellence while striking a balance between classic workwear and being on trend. The oldest employer in Bristol, Tennessee, the storied L.C. King factory and retail store is located steps from State Street and is a beloved part of Bristol’s iconic and deep-rooted history. Born out of a need for rugged, durable workwear that could withstand the rigor and daily demands of farming and hunting, L.C. King’s first clothing line, Pointer Brand, was inspired by Landon Clayton’s King’s champion bird dogs. Rebranded in 2006 as simply L.C. King, their classic triple-stitched overalls, chore coats, low-back suspenders, and 5-pocket jeans are more popular than ever, frequently worn by some of the hottest music artists in the Americana roots genre. One of the last remaining sewing factories in America to make its own brand, L.C. King remains synonymous with durability, heritage, and authenticity. While they frequently collaborate with designers around the world, their clothing is widely worn and recognized by those living and working in Bristol and the South, as well as the Birthplace of Country Music and Bristol Rhythm and Roots Reunion communities.
While Jack King grew up in Bristol, he never envisioned himself working at L.C. King. A gifted athlete and student, King was on the swim team and attended the University of Georgia, graduating with a degree in accounting. Following graduation, he worked as a tax accountant in Atlanta for 12 years before getting a phone call from his father asking him for help with the factory. He explained his journey from accounting to sewing, “I was a tax accountant and I had never anticipated ever coming here to the factory. That just was not part of what was going on with me and my life. Then my dad had a health issue and called me up and said he needed help. And so my first response was, ‘Well, if you’re calling me, you must be in pretty bad shape.’ And he was. So I came up and spent, believe it or not, I spent 20 minutes with him and then got back in the car and drove home to Atlanta and told my husband that I’ve got to move and asked if he wanted to come up here to Bristol with me, and he said he did.”
Shortly after, King and his partner packed up their life in Atlanta and began their quest of being the fourth generation to run the sewing factory that is L.C. King Manufacturing. However, while King had been successful at most things in his life, this particular challenge came with a learning curve. “All of a sudden I’m thrown into this and I made a lot of mistakes at the beginning. I wear them proudly – lessons learned and scars and tears and things that happen when you’re trying to teach yourself something that you never participated in before. So the first thing I decided to do once I completely failed at everything else was put myself on the sewing floor. I asked one of the supervisors to give me a job. I realized that I couldn’t understand why the women and the men upstairs on the sewing floor had the issues, complaints, or successes that they had until I experienced what they were experiencing.
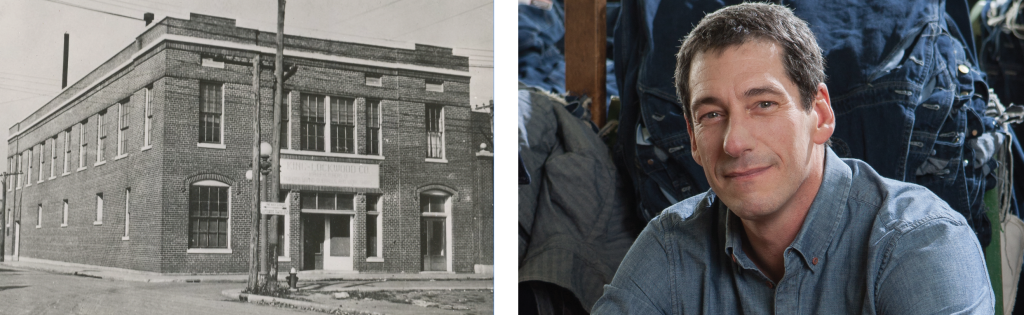
“So, Mary, the supervisor of the parts department, gave me the job of making the low back suspender. There are four separate steps to making the suspender. She taught me all the different steps, from making and cutting the banding to inserting the elastic in the top part of the suspender, and then braiding it and attaching the bottom part of the suspender. Now 25 years later, I’m the most prolific suspender maker at L.C. King; that’s a job I still have today. I’m the guy that makes the low back suspender. It’s my favorite item to make because it has the L.C. King imagery on every single piece. As my hands are placing the elastic into the garment, I’m actually putting, I’m sealing, the name of the factory into the garment in every piece I make.”
This shift in his managerial approach was a game changer for King and became the key to his successful transition at the factory. It has since become part of his daily routine, establishing him as a valued team member on the sewing floor and an advocate for his employees. It’s time well spent that seems to be part meditative and part strategic and gives him another layer of investment and pride in the production process. “I start my day sewing for about an hour and a half, and I can get a good chunk done during that time. It just sets the tone for the sewing floor, sets the tone for my day. By putting myself with the sewers at the beginning of the day, I now know how the day’s going to go. I am aware of different issues that certain machines have that the mechanic needs to address, as well as certain issues regarding production cuts and how they’re moving across the floor. I know what’s going on on the sewing floor that day and what’s going to happen for the next 10 days, as clothes start being put together. That’s something I’m thankful I did because I never would’ve known all the different issues that the men and women have on the sewing floor, but it’s so much more than that. I actually get to participate in the making of the garments that we sell here. And that puts a little pride in the product that we deliver.”
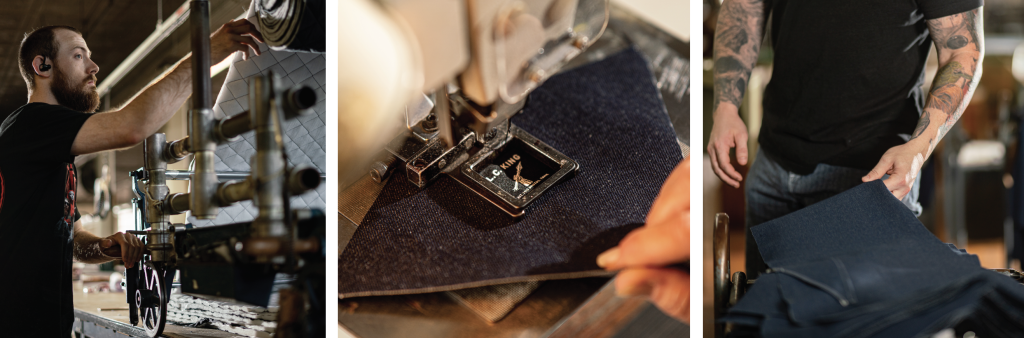
Made 100% in America and sourcing the majority of fabric and materials in the South, L.C. King provides a classic alternative to fast fashion. With all clothing hand cut and sewn on-site, customers visiting the retail store can have purchases tailored while they wait free of charge. They offer exceptional clothing that will likely last a lifetime, with some products such as the chore coats being heirloom quality. King takes pride in not only the quality of their clothing but the rich story behind each item, “We provide a garment that has a story behind it with its authenticity and its construction. Not only does the buyer create memories while wearing our clothing, but there’s a broader story there. The clothing our customers are wearing comes from a factory that’s been in existence for over 100 years. It likely has been made by a person who has been working in this factory for as many as 40 years. It was made almost with the exact same machines that were in place in the 1950s. In fact, the overalls and the low back suspender straps are cut using a cutting machine that came in here in 1918 that we still use today. Nine times out of ten, when the stuff comes from overseas, you have no clue who has made it. You have no idea what kind of factory it came out of. It’s just a piece of clothing that can be easily discarded, but something that’s made by L.C. King, it’s got heritage, it’s got authenticity. We take such pride and care in making sure we make a really great jacket or jeans.”
It’s not unusual for long-time customers to contact the retail store and begin the conversation with, “I’ve had this pair of overalls for over 30 years, and I’m looking to replace it. A lot of our older returning customers will say, ‘I’ve owned this coat for 20 years. I’ve had these overalls for 30 years, and I’m looking to replace them. Or ‘I’m looking for something similar to what these are.’” King explained that while all their clothing remains both functional and stylish, they’ve changed very little in design over the years. “We can confidently tell customers that we’ve got that overall because we’re still making it today. Regarding the chore coat and the barn coat, the pattern has changed just a little bit, but not a lot on the overalls and carpenter jeans. The carpenter jean has a lower rise than what we used to make in the fifties, but I’ll say this, the overall that we made in the forties and the fifties is the exact same overall that we make today – the exact same overall. And how I know that is, we have the original pattern pieces that were cut out of plastic that you would lay out by hand that we then digitized and put into a computer.”
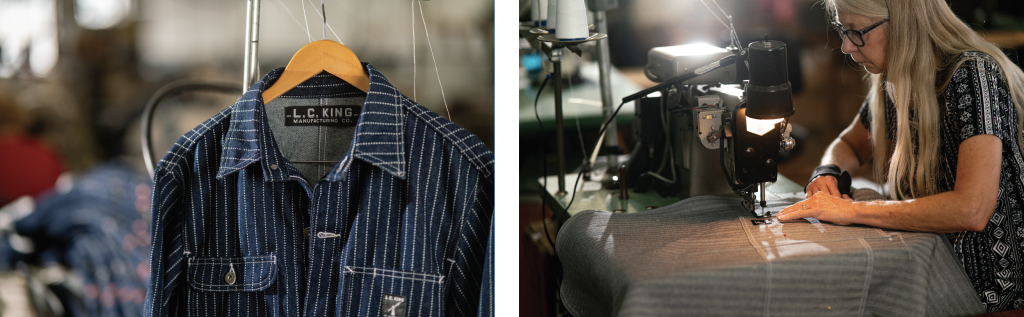
Albeit classic, functional, and durable clothing, the L.C. King brand is well-known and respected by those in the music industry, frequently outfitting artists and musicians because of its close connection with the Birthplace of Country Music. If you visit Bristol, particularly during the Rhythm and Roots Reunion festival, you’re likely to see L.C. King everywhere. Not only are several artists such as Amythyst Kiah, Moon Taxi, and Folk Soul Revival loyal to the brand, but during the 2013 festival St. Paul and the Broken Bones chose to film their video for “Let it Be So” in the sewing factory. And if you have a keen eye for detail, you might catch the keyboardist for Kid Rock or the guitarist for Luke Combs sporting the L.C. King logo as well.
I asked King what he would recommend to someone buying their first piece. While the low back overalls are their most popular item, King suggested the Brown Duck Chore Coat, one of their best-selling jackets since the 90s. “It is utilitarian in its design and extremely functional in how you wear it and what you can get out of it. It’s got these great patch pockets on the front. It’s got an inside pocket should you want to put your cell phone on the inside – all that kind of stuff. It is roomy and you look so tasteful in public. So that, by far, is the garment. And so you wear it fall through winter and into the spring, and then you give it a break during the summer. Then fall comes around and all of a sudden you see your old friend, the Brown Duck Chore Coat, and say, ‘Hey man, I was rocking that thing last year. I’m in it again this year!’ It’s just a great jacket to wear. It’s lightweight and it’s just got great construction and character. But most of all, and I don’t mean to keep stressing this, but you look tasteful in public wearing it. And that’s my thing. I really want someone to look really nice in public when they’re wearing the clothes that we make.” And while they rarely introduce new designs, this November there will be a limited one-time run of a new jacket, the Gibson, which is similar in design to their western jacket.
Jack King is proud of the brand his family has built over the past 110 years and he has no plans of slowing down. Just the other day he was standing in line at the grocery store when someone looked at his t-shirt and said, “Oh, what does L.C. King make?” Before he could respond, a younger girl answered, “They make the overalls, jackets, and jeans.” The sweetness of the moment was not lost on King who is grateful for loyal customers and brand recognition, “The lady had just moved here and really had no idea what we were, but the younger person standing right next to her knew exactly who we were. It meant everything because the younger generation recognized us, which means we are starting to be part of their life and the memories that they’ll make. I see people wearing our overalls or jackets all the time, and I always think: That person has taken this time to support the factory where they live. And that just gives you a sense of pride because we’ve taken the time to make sure that we’ve made the best quality garment that we can, and now here’s someone actually appreciating our skills and efforts. It just means everything.”
At the end of the exchange, the women asked King, “What do you do?” King simply responded, “I’m on a sewing machine.”
“I’m a guy who works at the company,” King explained to me. “I love that completely different sentence because that’s really who I am. I’m a person who works at L.C. King versus a person who actually owns L.C. King.”